David Trumper resumes & CV records
Resumes
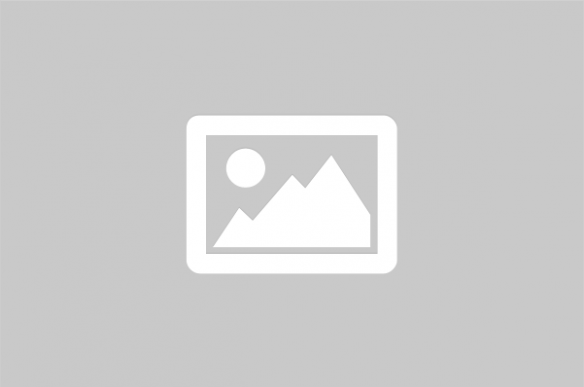
601 Center St, Phoenixville, PA 19460 (610) 917-0153 (610) 917-9712 (610) 933-1945
21 Main St, Phoenixville, PA 19460 (610) 917-0153
Plaistow, NH
228 Bala Ave, Bala Cynwyd, PA 19004 (610) 664-2352
Lyman, NH
Cleveland, OH
Mentions for David K Trumper
NOTICE: You may not use PeopleBackgroundCheck or the information it provides to make decisions about employment, credit, housing or any other purpose that would require Fair Credit Reporting Act (FCRA) compliance. PeopleBackgroundCheck is not a Consumer Reporting Agency (CRA) as defined by the FCRA and does not provide consumer reports.