Dipankar Pal resumes & CV records
Resumes
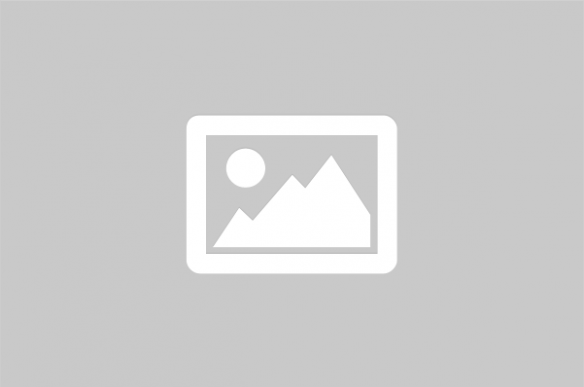
Systems Engineer
Systems Engineer Ge Aviation Oct 2001 - Nov 2006
Lead Engineer
Doctorates, Doctor of Philosophy, Philosophy
Education
Environment
Science and Technology
Arts and Culture
Health
Hindi
Bengali
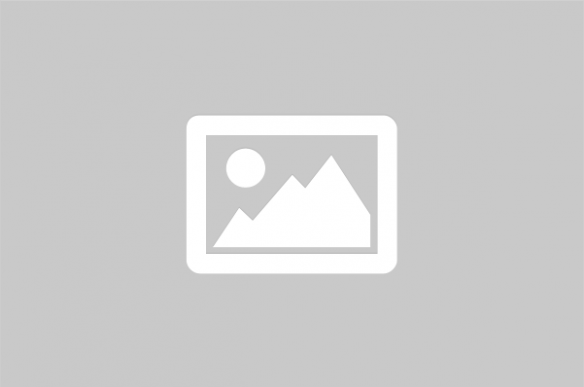
Associate Director, Fluid-Thermal Engineering
Associate Director, Fluid-Thermal Engineering Ge Power Jun 2015 - May 2017
Senior Systems Engineer Ge Power Dec 2006 - Jun 2015
Technical Leader Heat Transfer Ge Aviation Oct 2001 - Dec 2006
Lead Heat Transfer Engineer Mtu Aero Engines Oct 2000 - Nov 2001
Analytical Engineer University of Mississippi May 1997 - Sep 2000
Post Doctoral Researcher
Doctorates, Doctor of Philosophy, Philosophy
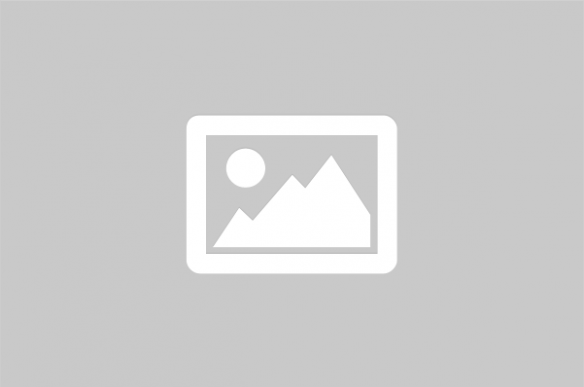
Dipankar Pal
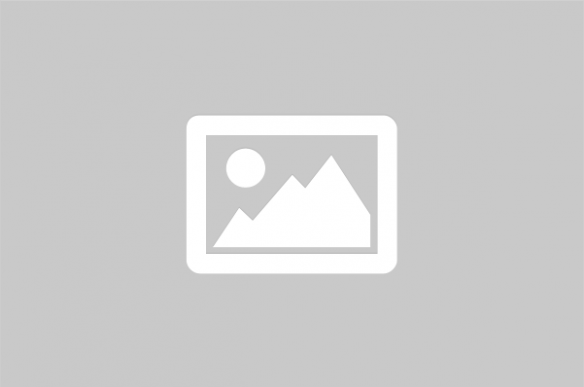
Dipankar Pal
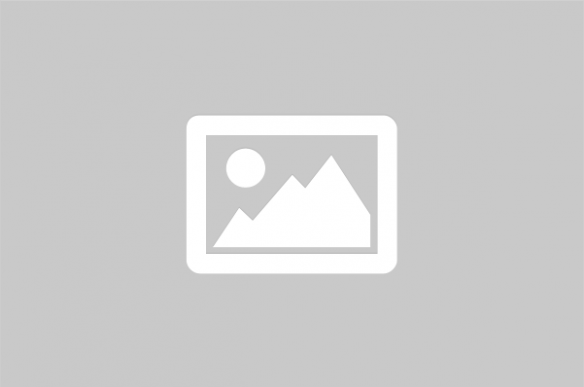
Dipankar Pal
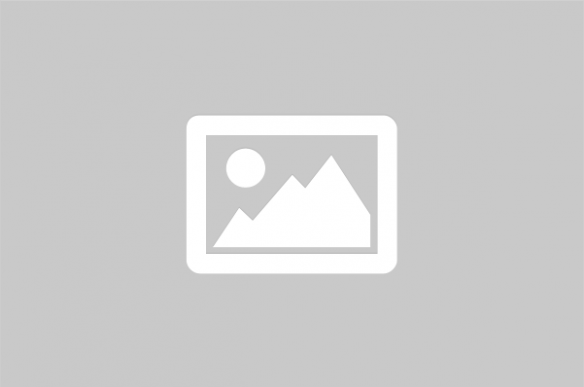