Dwight Stephenson resumes & CV records
Resumes
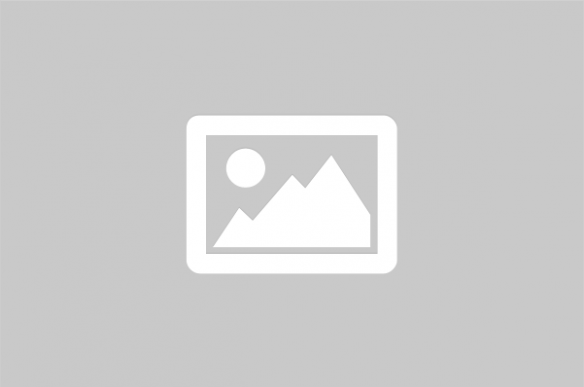
692 Crowe Rd, Columbus, MS 39702 (662) 328-0409
Detroit, MI
2509 5Th St, Milwaukee, WI 53212 (414) 372-9714
Indianapolis, IN
Midland, MI
Mississippi State, MS
Mentions for Dwight L Stephenson
NOTICE: You may not use PeopleBackgroundCheck or the information it provides to make decisions about employment, credit, housing or any other purpose that would require Fair Credit Reporting Act (FCRA) compliance. PeopleBackgroundCheck is not a Consumer Reporting Agency (CRA) as defined by the FCRA and does not provide consumer reports.