George Carini resumes & CV records
Resumes
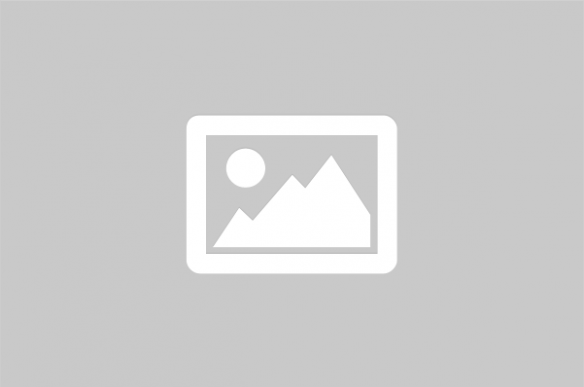
Proprietor
Location:
Carnegie, PA
Industry:
Glass, Ceramics, & Concrete
Work:
Proprietor
1660 Norsen Dr, Pittsburgh, PA 15243 (412) 276-6818
729 Washington St, Carnegie, PA 15106 (412) 276-5251
Mentions for George F Carini
NOTICE: You may not use PeopleBackgroundCheck or the information it provides to make decisions about employment, credit, housing or any other purpose that would require Fair Credit Reporting Act (FCRA) compliance. PeopleBackgroundCheck is not a Consumer Reporting Agency (CRA) as defined by the FCRA and does not provide consumer reports.