Gilbert Abrams resumes & CV records
Resumes
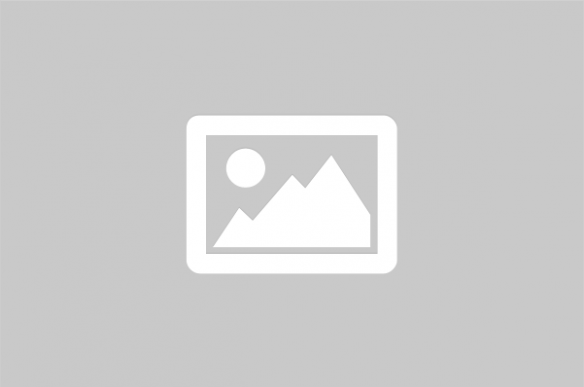
Gilbert Abrams
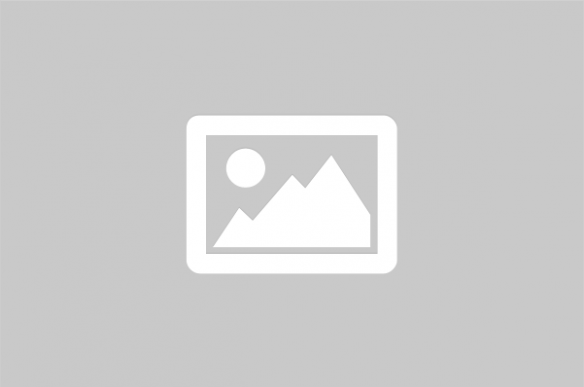
Wealth Management Advisor Assistant At Northwestern Mutual
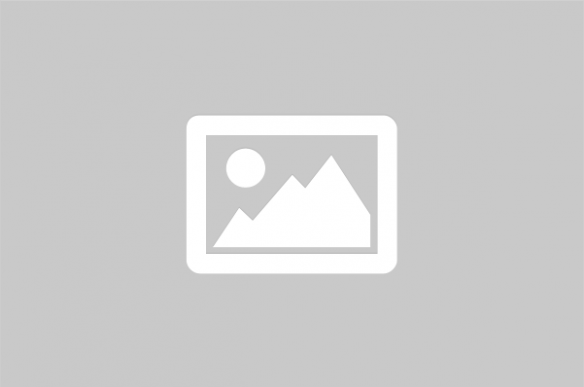
Gilbert Abrams - Lynbrook, NY
Work:
NCR Corporation - Hicksville, NY 2008 to 2013
Customer Engineer J&C Autoworld LLC - Amityville, NY 2007 to 2008
Automobile Salesperson Falcon Datacom Inc - Brooklyn, NY 2005 to 2007
Cable Installation Technician Gil's Computer Services - Richmond Hill, NY 2001 to 2005
IT/Consultant
Customer Engineer J&C Autoworld LLC - Amityville, NY 2007 to 2008
Automobile Salesperson Falcon Datacom Inc - Brooklyn, NY 2005 to 2007
Cable Installation Technician Gil's Computer Services - Richmond Hill, NY 2001 to 2005
IT/Consultant
Education:
The College of Staten Island - Staten Island, NY 1982 to 1984
information technology and business
information technology and business
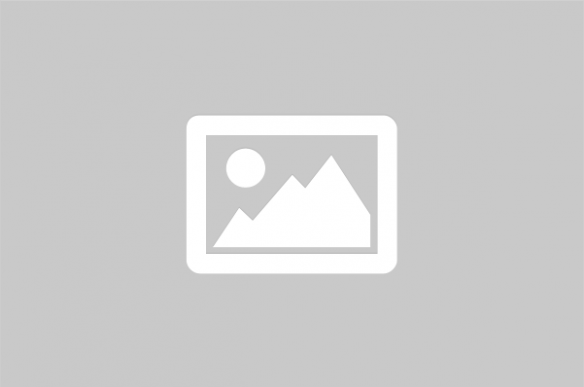
Independent Construction Professional
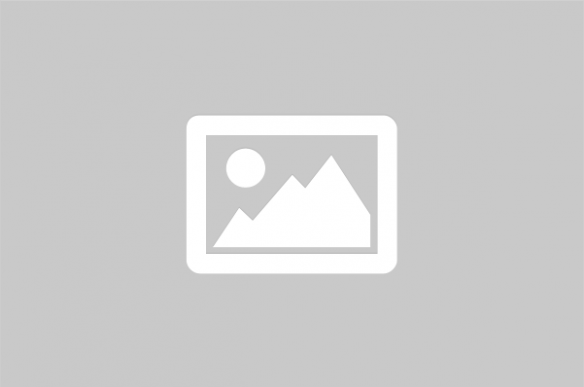