Jack Ayers resumes & CV records
Resumes
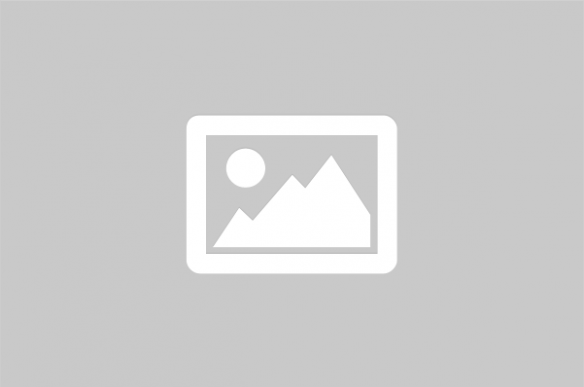
Jack Ayers
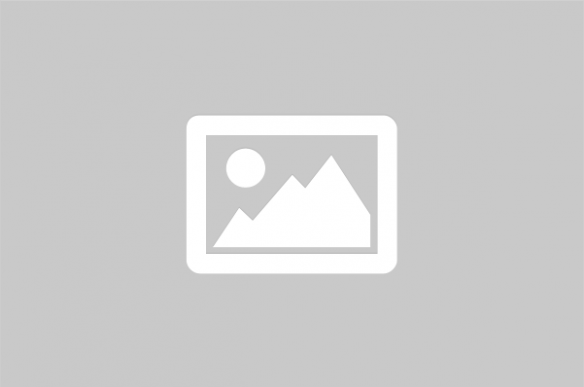
Jack Ayers
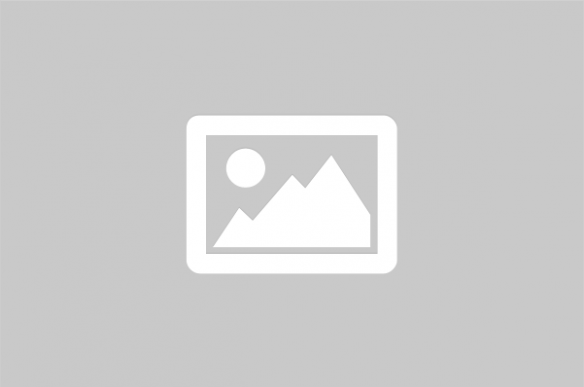
Jack Ayers
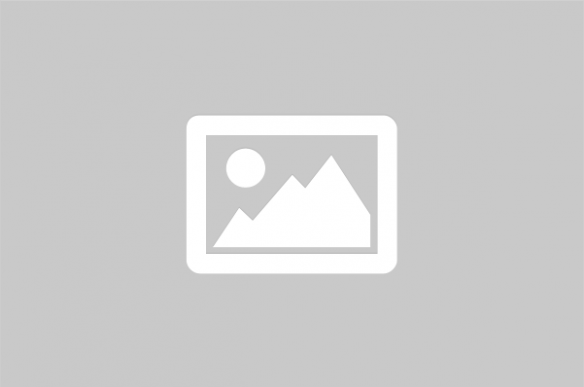
Jack Ayers
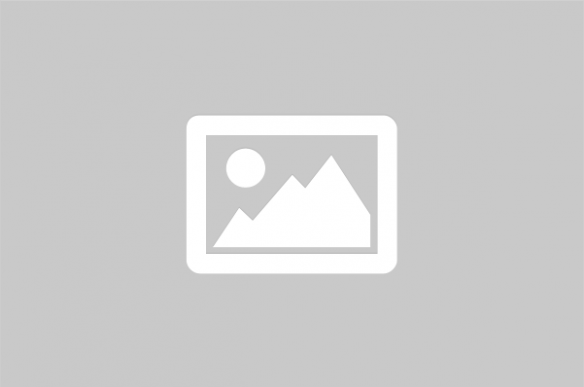
Vancouver, WA
1020 Arcadia Dr, Roseburg, OR 97470 (541) 677-6320
1520 Arcadia Dr, Roseburg, OR 97470 (541) 677-6320
1756 Starmer St, Roseburg, OR 97470 (541) 957-0574
Oakton, VA
Bowie, MD
Mentions for Jack D Ayers
NOTICE: You may not use PeopleBackgroundCheck or the information it provides to make decisions about employment, credit, housing or any other purpose that would require Fair Credit Reporting Act (FCRA) compliance. PeopleBackgroundCheck is not a Consumer Reporting Agency (CRA) as defined by the FCRA and does not provide consumer reports.