Liem Truong resumes & CV records
Resumes
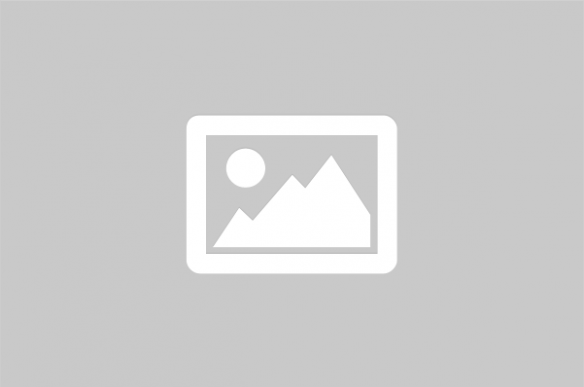
Liem Truong
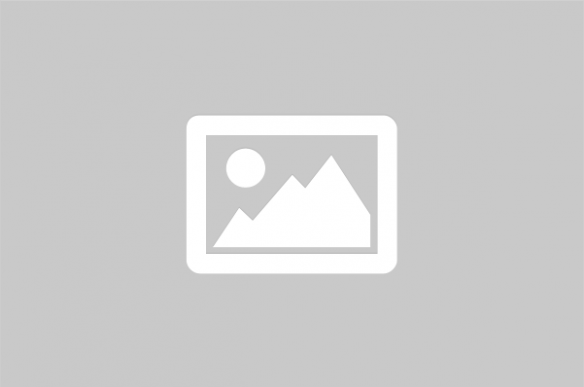
Liem Truong
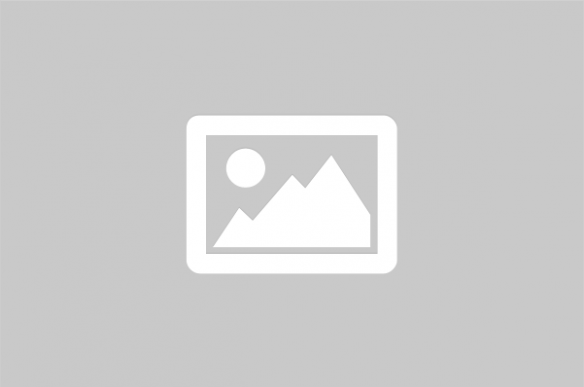
Liem Truong
Location:
United States
Greenville, NC
Goldsboro, NC
3117 Enterprise Dr APT B1, Wilmington, NC 28405 (910) 409-2059
Sunland, CA
Charlotte, NC
Glen Allen, VA
Mentions for Liem V Truong
NOTICE: You may not use PeopleBackgroundCheck or the information it provides to make decisions about employment, credit, housing or any other purpose that would require Fair Credit Reporting Act (FCRA) compliance. PeopleBackgroundCheck is not a Consumer Reporting Agency (CRA) as defined by the FCRA and does not provide consumer reports.