Peter Dinardi resumes & CV records
Resumes
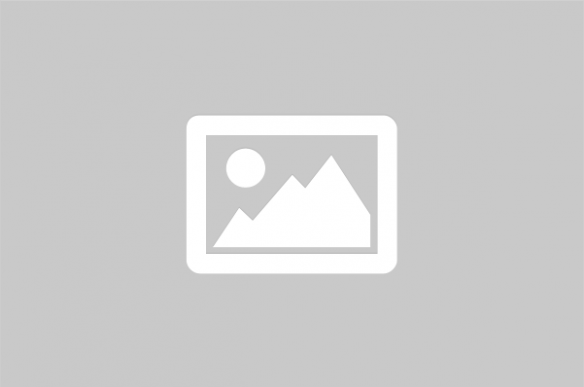
Peter Dinardi
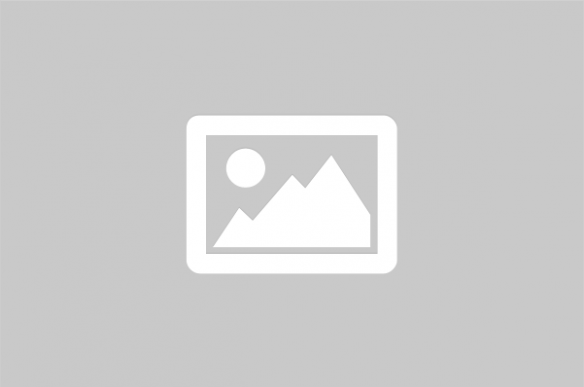
Peter Dinardi
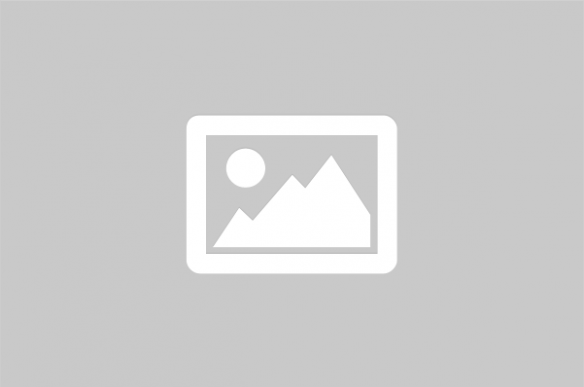
Monroe, MI
Myrtle Beach, SC
18881 Mayfield St, Livonia, MI 48152 (248) 426-9652
Wake Forest, NC
Waterford, MI
Minneapolis, KS
Clarkston, MI
Parma, OH
Oakland, MI
Mentions for Peter C Dinardi
NOTICE: You may not use PeopleBackgroundCheck or the information it provides to make decisions about employment, credit, housing or any other purpose that would require Fair Credit Reporting Act (FCRA) compliance. PeopleBackgroundCheck is not a Consumer Reporting Agency (CRA) as defined by the FCRA and does not provide consumer reports.