Russell Nippert resumes & CV records
Resumes
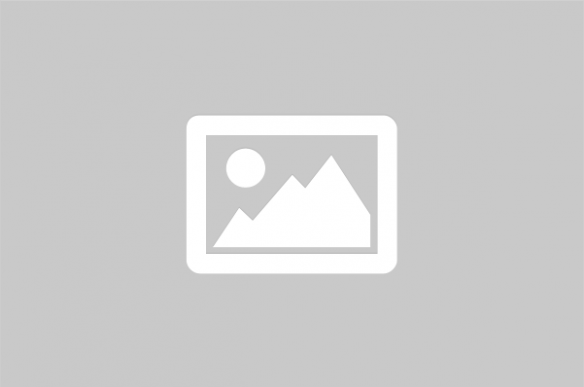
5735 Liscarroll Pl APT 31-573, Dublin, OH 43016
3177 Melbury Dr, Columbus, OH 43221 (614) 451-9493 (614) 777-6324
2504 Danvers Ct, Upper Arlington, OH 43220 (614) 451-9493
9265 Garden Pointe, Fort Myers, FL 33908 (239) 590-9736
Captiva, FL
5735 Liscarroll Pl, Dublin, OH 43016 (614) 451-9493
Mentions for Russell A Nippert
NOTICE: You may not use PeopleBackgroundCheck or the information it provides to make decisions about employment, credit, housing or any other purpose that would require Fair Credit Reporting Act (FCRA) compliance. PeopleBackgroundCheck is not a Consumer Reporting Agency (CRA) as defined by the FCRA and does not provide consumer reports.