Tony Salemi resumes & CV records
Resumes
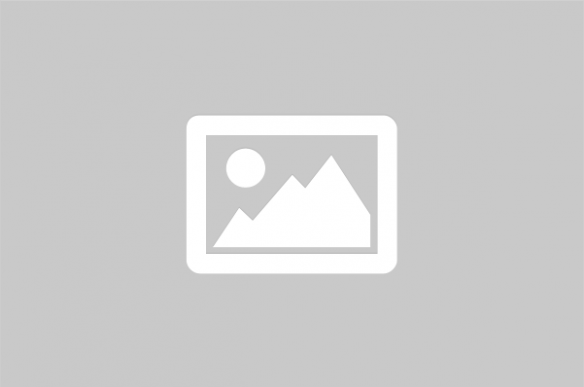
Tony Salemi
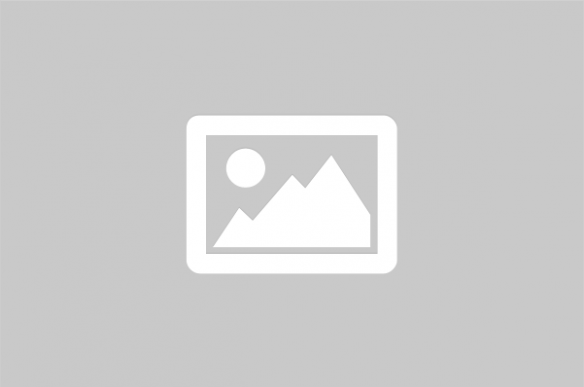
Tony Salemi
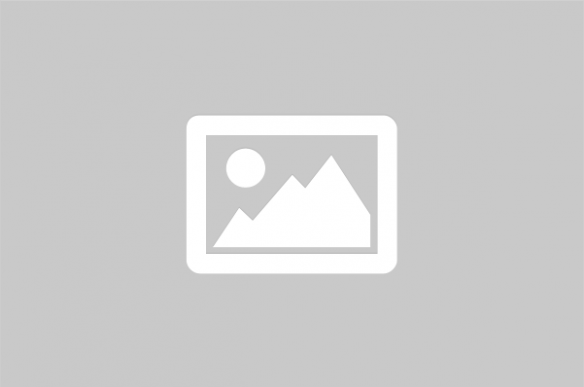
4705 Sawgrass Dr, Pittsfield Township, MI 48108 (734) 995-1549 (734) 623-4243
3832 Highlander Way W, Ann Arbor, MI 48108 (734) 623-4243
2514 Bunker Hill Rd, Ann Arbor, MI 48105
3622 Tanglewood Ct, Ann Arbor, MI 48105
7903 Granville Dr, Ft Lauderdale, FL 33321 (954) 724-2866 (954) 724-7521 (954) 247-9581
Tamarac, FL
Ypsilanti, MI
Massapequa Park, NY
Detroit, MI
Mentions for Tony D Salemi
NOTICE: You may not use PeopleBackgroundCheck or the information it provides to make decisions about employment, credit, housing or any other purpose that would require Fair Credit Reporting Act (FCRA) compliance. PeopleBackgroundCheck is not a Consumer Reporting Agency (CRA) as defined by the FCRA and does not provide consumer reports.